旋挖钻机在大直径硬岩地层施工工艺的研究
2014-12-30
1049
0
核心提示:张继光 罗菊 刘永光
(徐州徐工基础工程机械有限公司,江苏徐州 221004 )
摘 要:旋挖钻机在硬岩地层钻进时,经常出现钻进
张继光 罗菊 刘永光
(徐州徐工基础工程机械有限公司,江苏徐州 221004 )
摘 要:旋挖钻机在硬岩地层钻进时,经常出现钻进困难、钻进效率低、机器故障率高等问题,导致施工效率较低。本文通过对分级钻进施工工序、分级方法的理论研究,提出了具体的施工工艺方法,并借助徐工XR460D旋挖钻机在徐州三环路高架桥中的施工进行实验验证,经验证此施工工艺可大大提高大直径硬岩钻进效率,极具推广意义。
关键词:旋挖钻机;大直径硬岩钻进;分级钻进;筒钻取芯
1、前言
旋挖钻机在大直径坚硬岩层钻进时,常出现钻进难、钻进效率低、机器故障率高的现象,导致旋挖钻机在大直径入岩施工中经济收益差,施工推广难等难题。解决旋挖钻机大直径硬岩地层钻进难,钻进效率低的问题,对旋挖钻机在硬岩层钻进施工的推广具有十分重要的意义。
本文结合徐工XR460D旋挖钻机(钻机性能见表1)在徐州三环路高架桥中的施工进行研究。此工况地质条件较复杂,岩层主要以灰岩为主,灰岩裂隙中等发育,且灰岩中溶洞发育多以中小型溶洞为主,灰岩最大饱和单轴抗压强度达90Mpa、钻孔直径在2m-3m之间,钻孔深度30m左右,施工难度较大,国内类似工况施工因为效率低、机器故障率高等问题,用户不能得到满意的经济收益,致使旋挖施工工法未在该工况施工中得到推广。
表1 钻机性能
2、目前技术现状
目前旋挖钻机在解决大直径硬岩地层钻进中,大多采用以下施工工艺:
1)使用钻具组合施工工艺。即先使用筒钻钻进,然后使用螺旋钻头破碎,最后使用双底板捞砂斗捞渣。此种施工工艺,需频繁更换钻头,钻进辅助工时较多,导致效率较低,且截齿消耗量较大。
2)采用在大直径桩孔的中心先用旋挖钻机合理“取芯”,再用冲击钻冲击成孔的方法。这样的组合方式大大加快成孔速度,但施工中必须配置旋挖钻机与冲击钻,任何单独一台设备无法有效施工。
3)采用分级钻进施工工艺进行钻进。该工艺对大直径硬岩地层钻进较为有效,但由于目前研究及实践较少,存在分级方式混乱、不能合理使用钻头、没有规范的操作流程等问题,导致分级钻进施工工艺的优势无法发挥出来。
3、分级钻进的研究
通过对原有工艺的研究,发现分级钻进施工工艺极具研究价值,其工艺核心原则是将单次成孔较困难的大直径硬岩钻进,分成几个层次等级钻进,有效降低单次钻进难度,并通过各层次等级钻进间的相互影响,减小钻进难度,最终实现较大直径的钻进。
但由于目前对于分级钻进的研究还较少,理论缺乏,导致实际施工中施工工序、分级方法混乱,分级钻进的优势难以发挥,因此对于分级施工工艺的合理优化,将是解决大直径硬岩地层钻进的问题的核心。
3.1分级钻进理论研究
3.1.1分级钻进施工工序研究
通过对分级钻进的现场资料收集及理论计算,将分级钻机各级钻进时钻具使用及操作流程整理如下(如图1所示):
图1 分级组合钻进示意图
第一步:先使用小孔径岩石筒钻钻进,并配合小孔径捞砂斗清渣,反复配合钻进到设计终孔位置。
第二步:使用大孔径岩石筒钻进行扩孔,钻进到一定深度后,扩孔切削下来的碎石,会将小孔径空间填满。
第三步:当小孔径空间被填满后,使用小孔径捞砂斗进行清渣,然后再使用大孔径岩石筒钻继续扩孔,如此反复,最后使用大孔径捞砂斗清孔到设计孔深位置。
3.1.2分级钻进方法研究
如何对桩孔进行分级设计一直是分级钻进研究的瓶颈,分级过少将导致每一级钻进难度增大,施工效率降低;分级过多将导致钻具配置增加,施工流程复杂,施工效率降低。只有最合理的分级才能将分级钻进的优势真正发挥出来。
根据J• Brych自由面岩石破碎理论,当旋转钻头附近存在有自由面时,钻头侵入时岩石会产生侧旁的破碎,有利于提高钻头入岩效率。钻头离自由面槽的距离在10cm之内时,钻进效率较高(如图2所示)。
图2 分级原理图
为保证扩孔钻进时,小孔径破碎所形成的自由面,对扩孔钻进的有益影响,需保证筒钻内齿距小孔外径在10cm左右,加上筒钻破碎时自身所形成的12cm的圆环槽,便可确定分级方法。
由以上理论确定的每相邻钻孔直径差控制在44cm左右,但上述理论是建立在岩石完整的基础上,由于实际工况中,岩石存在一定破碎,且破碎程度差异较大,故实际分级时每相邻钻孔直径差控制在40-70cm,具体选择需根据地质资料。
3.1.3分级钻进时操作原则
1)第一级钻进时筒钻取芯优先的操作原则;
2)扩孔钻进时使用岩石筒钻原则。如果使用双底板扩孔钻进,边齿受力,中心悬空,会出现钻头易磨损的问题,而且使用岩石筒钻扩孔钻进比使用双底板扩孔钻进施工效率提高了2倍;
3)使用大孔径岩石筒钻进行扩孔原则。根据已施工小孔所容纳的土石方量与扩孔切削的碎石土石方量,计算当小孔空间填满时,大孔能扩孔的深度,合理安排扩孔钻进深度。
3.2分级钻进现场实验
通过以上理论研究,对徐工XR460D旋挖钻机在徐州三环路高架桥施工工程,进行现场验证(如图3所示)。
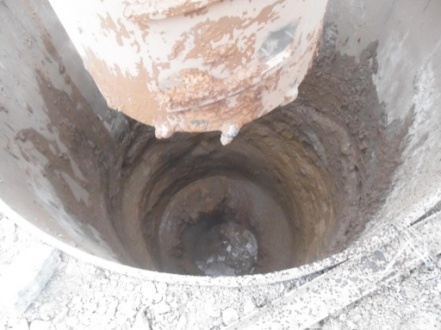
图3 现场分级钻进图片
通过大量试验,最终找出适合XR460D在不同强度灰岩的最佳分级方法(如表3所示),
表3 分级方式

由表可看出,岩石强度越小分级次数越少,分级极差越大,最大可达70cm;岩石强度越大,分级次数越多,分级极差越小,分级极差应控制在30-40cm左右。通过上述实验 情况可以看出,实际分级方法与理论提出的40-70cm极为吻合。
现场施工中,严格按照理论提出的分级工序进行施工,施工中工序流畅,各工序衔接较好,大大减少了因频繁更换钻头、工序衔接不上、现场施工混乱引起的施工时间浪费,大大提高了钻进效率。
3.3 分级钻进施工效果
采用上述分级钻进施工工艺,XR460D旋挖钻机于2012年7月在徐州三环路高架桥工地完成了250小时施工作业。在不到一个月的时间里,成功施工直径2.2米桩孔30余根,取出岩心硬度最高达到90MPa,为旋挖钻机在大孔硬地层的施工积累了宝贵经验。
而采用原有施工工艺,旋挖钻机基本无法完成在如此强度、大直径地层施工。此工艺的研究大大提升了旋挖钻机在大直径硬岩地层中的钻进优势。
4、结论
通过分级钻进施工工艺的合理优化,提出的施工工艺在实际施工中表现出较大的优势,极具推广意义。由于借助具体工程进行实验研究,受实验投入限制,无法配置所有规格钻头进行分级钻进对比研究,后期还需借助不同工程进行逐一验证。
此工程通过分级钻进的合理应用,研究国产旋挖钻机在大孔径、高硬度地层的施工效率,提升了旋挖钻机在大直径硬岩地层中的钻进优势,推动了旋挖工法的普及。
参考文献:
[1] 宋刚.硬岩地层旋挖钻进组合工艺的研究与应用[J].施工技术,2011,40(2):72-74.
[2]孙秀梅,刘建福.坚硬“打滑”地层孕镶金刚石钻头设计与选用[J].探矿工程(岩土钻凿工程),2009,36(2):75-78.
[3]柳正刚.旋挖钻进工艺在高架桥桩基工程中的应用[J].山西建筑,2008(10):153-154.
[4]新型硬岩钻进双筒环形钻具的研制与应用[J].地质装备,2012(2):56-58.