富水区深基坑止水帷幕局部渗漏处理技术
2015-01-14
234
0
核心提示:摘 要:文章结合工程实例,针对松花江漫滩区高承压富水砂质地层条件下深基坑钻孔桩+二重管旋喷桩止水帷幕局部渗漏的原因进行了分
摘 要:文章结合工程实例,针对松花江漫滩区高承压富水砂质地层条件下深基坑“钻孔桩+二重管旋喷桩”止水帷幕局部渗漏的原因进行了分析,采取了地面垂直注浆封堵、探挖和桩间斜向注浆固结、钢板封闭、加强网喷和快速封底等处理措施,解决了深基坑止水帷幕局部渗漏的难题。
关键词:地铁车站;富水深基坑;止水帷幕;渗漏处理技术
1前言
近年来随着城市的建设发展,轨道交通工程建设的步伐明显加快。地铁工程建设中所涉及的深基坑工程具有基坑面积大、开挖深度深以及周边环境复杂等特点,施工安全质量受到社会各界的广泛关注。基坑,尤其是富水区深基坑,止水帷幕的选择十分关键,不仅影响到工程的顺利进行,还直接关系到生命财产安全。
在城市轨道交通工程建设初期,由于缺乏相关工程经验、对地质水文环境掌握深度不够,以及过于冒进等因素的影响,且存在着对各种工法的尝试和验证的考虑,往往存在选择止水帷幕形式不当而造成基坑开挖施工困难,严重威胁到施工及周边环境安全,因此需要对止水帷幕局部渗漏的处理作进一步的研究。
2工程概况
2.1工程简介
哈尔滨地铁一号线某车站为地下二层岛式站台车站,基坑长239.4m、宽19.4m,小里程端基坑开挖深度为17.9m,围护结构深度为26.836m;基坑 标准段开挖深度为16.18m,围护结构深度为24.64m左右;大里程端基坑开挖深度为18m,围护结构深度为26.94m。
车站采用明挖顺作法施工,基坑围护结构设计采用φ800@1000mm钻孔灌注桩+φ1000@1000mm旋喷桩(二重管)止水帷幕形式,⑨粉质粘土层作为承压水隔水层,止水帷幕深入⑨层1m。施工完成后通过基坑降水及开挖情况显示,钻孔桩+旋喷桩止水帷幕形式在该地质条件下出现渗漏。后经论证,在原有止水帷幕外侧增加了一圈600mm厚与原围护结构同深的C30素混凝土地下连续墙,进行封闭止水。后期基坑开挖过程中降水仍然十分困难,且多次出现涌水、涌砂。
2.2工程场地的地质、水文条件
车站场地属于松花江漫滩地貌单元。松花江水位高程为118.95m,地面高程为119.72~120.74m。场地土层的工程地质参数如表1所示,地质剖面如图1所示。
由于工程处于松花江漫滩区,地下水丰富,补给速度快,平均渗透系数为72.74m/d,属透水—强透水地层。潜水水位高程为116.7m;微承压水水位高程为114.98m,水头高度为4.58m;承压水水位高程为112.64m,水头高度为22.64m,与松花江存在水力联系。
表1 场地土层的工程地质参数
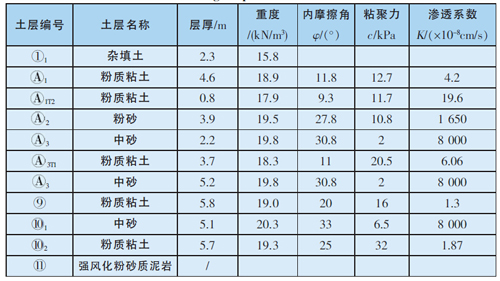
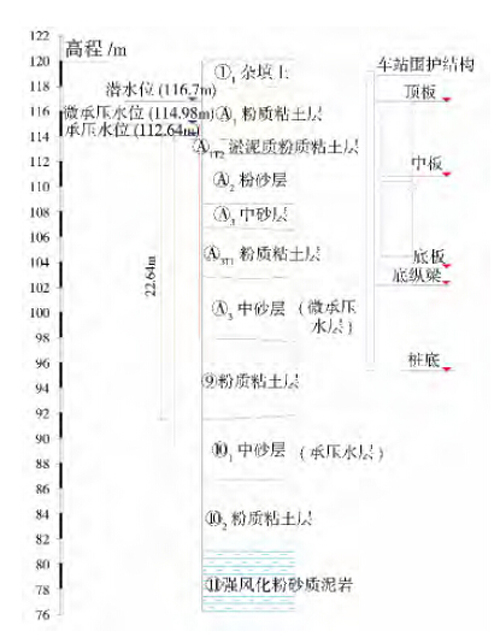
图1 典型地质剖面
3止水帷幕局部渗漏的原因分析
(1)通过车站基坑探挖及开挖情况可以看出,地面向下12m以下地层中开始出现粉砂、中粗砂层,并夹杂有粉质粘土层,同时砂层中含泥量也比较大,钻孔桩+旋喷桩止水帷幕与地连墙止水帷幕之间存在1.5m左右的原状土夹层;在基坑内疏干降水施工时,两道止水帷幕之间的原状土层中的水通过钻孔桩缝向基坑内渗流过程中,地层中的粉质粘土以及钻孔桩、地连墙施工的泥浆护壁存留的粉质粘土,在地下水渗流过程中在桩缝之间砂层表面形成了一层保护膜;基坑内地下水降至基坑底以下时,两道止水帷幕之间的原状土中的地下水只是少部分被排出;当人工清理桩缝之间的砂土时,保护膜遭到破坏后,桩背侧砂土连砂带水就会快速涌出,形成涌水、涌砂通道。
(2)两道止水帷幕之间存在1.5m左右的原状土夹层,而砂层的直立性比较差,素混凝土地连墙成槽及混凝土浇筑过程中存在坍塌的可能,会造成部分地下连续墙墙缝间出现夹泥夹碴,形成透水通道,当钻孔桩桩缝间存在薄弱位置或者空隙时,地下水就会通过渗水通道携带泥砂涌出。由于夹层的存在,漏水位置无法判断,不能准确找到漏水位置进行封堵止水。
(3)由于地下水具有流动性,旋喷桩施工期间,水泥浆液被携带距离较远,形成固结块,素混凝土地下连续墙施工期间部分位置会出现靠近基坑一侧土质偏硬、另一侧偏软的情况,造成地连墙成槽垂直度偏差较大,致使两幅墙接缝位置出现相互错位,止水性能较差。
(4)⑨粉质粘土层作为承压水隔水顶板,其均质性、深度、厚度等在基坑范围内存在偏差,对基坑止水性能有一定影响。地质条件的复杂多变、隔水层层厚较薄、止水帷幕未隔断承压水等因素也是基坑围护结构出现渗漏的一个原因。
(5)由于地质条件较差,砂层较厚,二重管高压旋喷桩施工质量较差,旋喷桩与钻孔桩之间无法形成充分咬合。
4处理方案
4.1钻孔桩与地连墙之间垂直插管注浆封堵
由于钻孔桩与地连墙之间存在1.5m左右的原状土夹层,而探挖期间夹层中的泥砂通过桩缝随水流出,为了分段阻隔地连墙渗漏时的通道、稳固两道止水帷幕之间夹层部分的土体,采用地质钻机引孔,立式注浆机对夹层中的土体进行垂直插管注浆固结。注浆孔位纵向间距为3m,插入深度为25m,采用425普通硅酸盐水泥,水灰比为1∶1,水泥浆与35Be°水玻璃浆液的比例为1∶1,注浆压力为0.5~1.0MPa,当出现返浆及注浆压力快速增长时向上提管0.5m继续。垂直注浆如图2所示。
图2 引孔注浆
4.2桩缝间探挖措施
当地面垂直插管分段注浆完成后,开始向下探挖。由于地质情况以及止水帷幕的特殊性,桩缝间采用人工探挖,探挖时附近备足砂袋、棉被、已经打好锚固孔的钢板(厚10mm、宽度为0.5m、长度为0.4m)及木楔子等应急物资。边探挖边用钢板进行封堵,防止探挖后在墙面出现涌水;桩缝逐缝分层探挖,探挖深度保持在开挖面以下1.5m左右,每层为30cm,随即采用电钻在钻孔桩桩体上钻孔,深度至少为10cm;打入膨胀螺栓或锚固钢筋,钢板紧贴桩体后打膨胀螺栓进行固定,同时在钢板与桩体之间的缝隙内灌入掺有“水不漏”堵漏剂的水泥砂浆,使桩缝与桩之间快速形成封闭固结体。探挖封闭方式如图3所示。
图3 桩缝探挖封闭
当桩缝间存在小的涌水时,直接将钢板顺着桩缝砸入土体中,上部打膨胀螺栓与桩体进行锚固,下部采用砂袋反压,然后在钢板上打孔,斜向插入注浆管注入改性水玻璃浆液进行固砂,如图4所示。然后探挖将该钢板下部固定,四周采用“水不漏”进行封闭,继续植入下一块钢板直到探挖至基坑底部以下为止。
图4 注浆固砂
当基坑出现较大涌水、涌砂时,在基坑内快速采用砂袋、棉被、水泥袋及排水管等应急物资进行反压,如图5所示。然后在涌水点对应基坑外侧采用高压旋喷桩及双液注浆综合手段使其形成固结封闭圈,达到封闭的效果。基坑外侧封水固结施工完成后,在坑内斜向插管注入化学浆液,逐层注入浆液,逐层揭开砂袋进行探挖,同步采用钢板封闭,直到基坑基底以下0.5m。
4.3桩缝间注浆固结
基坑探挖过程中根据地质情况,在基坑内通过桩缝间斜向插入3m长注浆管,对桩缝间的土体采用改性水玻璃浆液固结。
改性水玻璃施工控制参数为:
(1)注浆压力:P=0.3~1MPa。
图5 坑内反压封水
(2)施工浆液配制A液∶40Be°水玻璃与水按1∶3稀释;B液:98%浓硫酸与水按1∶6稀释;A液∶B液=1∶1。
(3)注浆深度:地面以下12m至基坑底以下1.5m,采用3m长的注浆管,与钻孔桩之间呈30°~45°俯角从桩缝间插入,顶部留出0.5m,连接三通管注入改性水玻璃浆液,如图6所示。
图6 桩缝间斜向注浆固结
基坑探挖过程中,对水采用堵排结合的方式进行控制。桩缝间采用钢板封闭后,设置一定数量的导流管,将桩缝间的水进行排出;同时将墙面的渗流水也采取导流措施,防止水顺墙面漫流,对下部土体产生冲刷、浸泡,造成失稳;开挖面的积水及时进行清理排除,避免长期浸泡。
4.4加强网喷施工
基坑开挖过程中及时挂设钢筋网片,喷射混凝土。由于地面以下12m围护结构止水效果相对较差,为了加强网喷施工封闭效果,提高整个网喷混凝土的抗变形能力,在地面下10m以下网喷施工时,每次网喷高度控制在1m以内,满铺挂设双层钢筋网,接头位置相互错开,并与在钻孔桩体上打入的锚筋连接牢固,随后及时喷射混凝土。
4.5快速封闭基底
由于深基坑地下水丰富、承压水水头高,需要不间断降低承压水水头(水头降低深度为5m左右)才能保证基底开挖后的稳定性。因此,车站基坑开挖到底一段后及时组织地勘、设计等单位分小段多次进行基底验收,并立即采用早强混凝土快速形成封闭,同时在混凝土中加入钢筋网。基坑四周2m范围做到随挖随封闭,同时将垫层厚度加厚至400mm左右。
4.6基坑外打设备用降水井
在基坑外侧打设一部分降水井作为备用井,当基坑内探挖出现渗漏水或涌水时立即启动备用降水井进行降水,减少基坑内的水压力,控制涌水的发生;基坑外降水的同时,加快基坑内的探挖,使用钢板使桩缝间快速形成封闭。
降水井施工时,地面以下12m范围井管采用水泥管,同时回填粘土;12m以下采用滤水管,井底封闭,四周回填碎石。井深为21.5m,将水管、水泵连接好,随时可以启动。基坑外降水时尽可能减少对粉土及粉质粘土层中水的影响,减少降水对地层的压缩变形。
5结论
在富水区,尤其是富水砂层地区,深基坑止水帷幕结构的选择与施工必须慎重,选择搅拌桩、旋喷桩等作为止水帷幕时必须提前检验确定其适用性,采用刚性接头地下连续墙并隔断承压水层为最优方案,可以大大降低基坑涌水、涌砂等安全风险事故的发生,有效保证施工安全、质量和进度。
通过采取探挖、桩间注浆固结、钢板封闭、加强网喷及基底快速封闭等措施,可以有效解决富水砂层地质条件下“钻孔桩+旋喷桩”止水帷幕局部渗漏基坑开挖问题,保证基坑施工安全。
作者:李义堂
转自《现代隧道技术》